In situ recovery
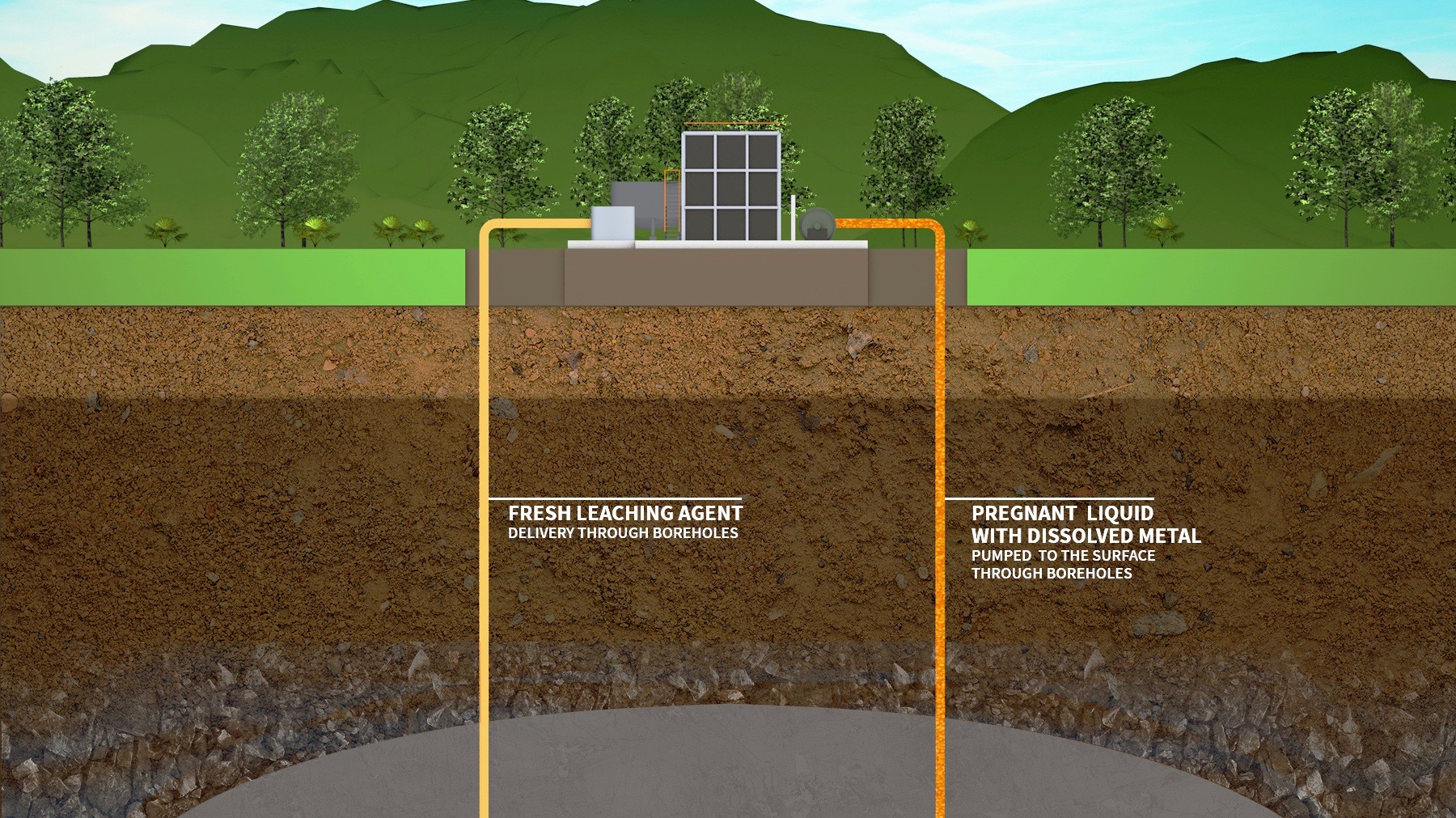
Challenge
Mining3’s ‘three pillar’ strategy aims to transform the mining industry through Lean Mining, In-Place Mining, and Sustainability through Technology. In Situ Recovery (ISR) is a low-impact method of metal recovery that involves the dissolving of a value metal from ore in situ into a fluid and pumping this fluid to the surface for processing. ISR forms one of the three methodologies that feed into Mining3’s In-place pillar, which aims to deliver: a small surface footprint, reduced tailings generation, low-environmental impact, high automation, and a low capital-intensity mine.
ISR has been demonstrated and commercially exploited before—for example, approximately half of the world’s uranium is recovered using an ISR approach. ISR has thus far been applied where ore body characteristics and local circumstances are favourable (access, geometry, permeability, leachability, etc.). However, the broader application to other commodities and ore types requires development and the demonstration of enabling technologies to further improve the potential and application of this approach, as well as to mitigate risks associated with each specific potential ISR project.
Research
There are a number of research and technology areas where we can and are working to facilitate the uptake of broader applications of ISR—for example, for hard or less permeable ores, smaller ore bodies, and/or ore bodies in sensitive situations.
These lines of work include: improved in situ ore body characterisation, improving the range of lixiviant system for consideration, conditioning the ore body for improved permeability and in situ liberation of target minerals, mitigating risk associated with loss of fluid containment/control, and realtime environmental and production monitoring/optimisation.
Mining3’s initial research program (with a focus on in situ liberation, value mineral access, and lixiviant system development) will be in place until 2021 and during this time it is envisaged that further collaboration, research opportunities, and industry deliverables will broaden the research and increase its impact.
How it works
With comparisons to ‘keyhole surgery for humans’, a successful ISR operation has a series of bore holes injecting and extracting fluids into and from the target ore body and the delivery and removal of these solutions through a pipe reticulation network to and from a small processing facility.
By careful selection of lixiviant to solubilise the values, metals can be extracted from suitable permeable ore bodies deep underground using conventional pumping technology with above-ground processing, and recycling of the lixiviant.
This approach is already being used commercially for uranium (and to a lesser degree copper) mining where the ore bodies are porous. Many of the earth’s resources are hosted in hard rock, which poses some challenges, but also some advantages in that lixiviants should be less likely to escape into the immediate environment.
Benefits
ISR avoids the removal of ore and overburden to surface dumps, stockpiles and operations. It eliminates comminution costs required prior to beneficiation, flotation, or leaching as well as the issues associated with the generation, storage and/or disposal of tailings.
Removal of the valuable components of a mineral deposit without physical extraction of the rock will have major economic and environmental advantages over current methods producing large amounts of waste and creating massive land disturbances.
ISR has the potential to deliver significant economic advantages through substantial reductions in mining costs—both capital and operational—and could allow for currently sub-economic ores to become attractive through low-cost, low-impact, selective mining.
- Decreased mine footprint
- Significant reduction in material movement
- No tailings generation/no surface tailings storage
- Less surface plant and site infrastructure
- Reduced requirement for heavy machinery
- No entry mining
- Low capital intensity and reduced operating costs
- Optimising margin over volume
- 60 per cent or more of the material remains underground
- Less energy required
Application of an ISR approach may be the step change needed to convert the untapped wealth of currently uneconomic ore bodies (already mapped) into attractive targets for metals recovery that drive value to economies and qualities of life.
Partners
The ISR initiative—originally borne out of CSIRO and now being led by Mining3—will be financially supported by a number of interested industry partners, research providers and, where possible, by government grants. A current project considering in situ liberation and optimised leaching systems is underway and additional sponsors are welcome. New initiatives (in critical areas described earlier) will be developed with industry and established as collaborative research and technology development opportunities in the near future.
Factsheet
For a printed version of this information, download the In Situ Factsheet.