Conveyor monitoring for wear detection
Pre-empting roller failure using fibre optics
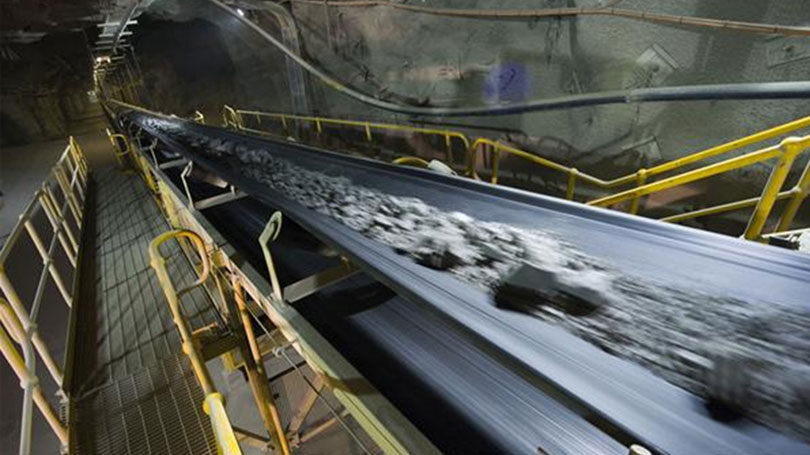
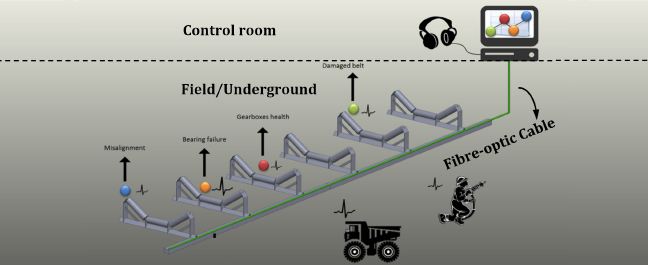
Challenge
Conveyor maintenance is a significant daily problem for the mining industry. Conventional methods of detecting bearing failure in conveyor rollers are unreliable, time-consuming and labour intensive.
Overland conveyors of 5 km are commonplace and 20 km conveyors from a local mine truck dump pocket to the processing plant are becoming increasingly common. A conveyor can have up to 7,000 bearings per kilometre. There have been several attempts to speed up and reduce the cost of monitoring all the bearings along a conveyor, and yet the original method of “walking the belt” observing and listening to the sound is still the most commonly used approach.
Research
An improved and near-commercialisation solution by Mining3 is an automated roller failure detector using fibre optics. The new technology is capable of constantly monitoring an entire conveyor system and alerting operators offsite to potential failures before they happen.
A fibre optic cable is run along the length of the belt with a single interrogator and analysis unit in a switch room. The technology works by recording the Rayleigh backscatter from inside the glass fibre. A powerful and very short laser pulse is transmitted along the single mode fibre, so it travels directly down the centre of the glass. Microscopic imperfections in the glass scatter the light in the same way that the earth’s atmosphere appears blue from sunlight being backscattered on oxygen and nitrogen molecules in the atmosphere. As the fibre moves, the backscatter varies and this is captured by a sensitive light sensor, amplifier, and digital to analogue converter (DAC).
The pulse-repetition-frequency of the laser and the sampling frequency are adjustable for conveyor distance, discrimination between idler frames and clarity of signal. When it is correctly set up, the interrogator is so sensitive it can detect the sound of single raindrops hitting the fibre.
It gathers data from every metre of the conveyor simultaneously. Samples are collected for several minutes after which they are processed in software. In less than an hour, every section of the conveyor has its own frequency plot image.
The Mining3 solution generates a “heat map” of the whole conveyor which shows hotspots in yellow and red where bearing wear has been detected by the software. One kilometre of conveyor can be tested in 10 minutes, from an operation centre, by inspecting the heat map and frequency plots at the hotspots and identifying worn bearings.
This technology is capable of:
- Detecting a broken ball or a cracked cage in a ball race
- Observing idler bearings as they progressively wear and track the development
- Predict potential bearing seizure and advise maintenance crews to change a roller at the next shut-down
Benefits
- Ideally timed roller change-out – not premature and not too late
- Reduced reliance on costly manual inspections
- Subjective approach and more formalised
- Easy installation and repair of the fibre optic cable
- Monitoring of the conveyor can be from an operation centre anywhere
- Captured data can be used to keep records and optimise maintenance strategies
- Maintenance requests can be generated automatically
and the data checked by an engineer in a remote location - Increased safety of personnel by reduced manual involvement
Status
Mining3 finalised a commercialisation agreement with the Ava Group who are the official developer and global distributor of the conveyor monitoring system. To talk to someone about purchasing or piloting the system, now known as The Aura IQ, contact AVA’s Group Head of Innovation, Extractives and Energy, Andrew Hames.
Factsheet
Access the latest Conveyor belt monitoring factsheet.