Detection of tramp metal
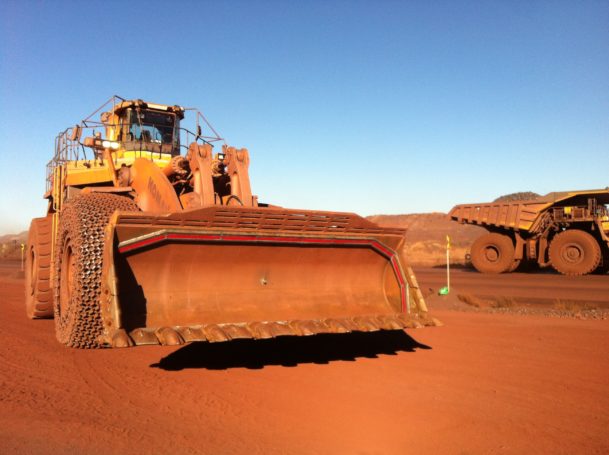
Challenge
Tramp metal such as bucket teeth, drill bits, bore crowns, tools, and more, left in mined material and stockpiles present a significant risk of blocking or damaging primary crushers.
In addition, high-energy ejection of tramp metal – specifically Ground Engagement Tools (GET) – from crushers, poses a serious safety risk to the operations staff.
Providing a simple, reliable, and cost-effective solution for the detection of tramp metal before it enters the crushing circuit can avoid a costly production delay and minimise safety risks.
Research
The patented uncrushables detection system incorporates a pulse induction metal detector fitted inside the bucket of a digging machine. Tramp metal objects entering the bucket at the commencement of the dig/dump cycle will trigger an alarm to the cab operator. Diversion or quarantine of the load can then occur.
This new technology encompasses an innovative combination of hardware and software to manage the challenge of detecting relatively small metal items using a detector that is itself embedded in a large steel bucket. Real-time detection notifications are fed to the cab operator who can take appropriate action to prevent the dispatch of the payload to crushers or other equipment susceptible to damage or blockages. The device’s detection algorithm performs self-calibration to adapt to changes in its environment.
The ground-breaking tramp metal detection approach requires minimal sensing equipment at the bucket. Commercial versions will discreetly integrate the detector coil into the bucket design for optimum protection and minimal interference with the material flow during digging and dumping.
With a remote interface, varying levels of system control such as detection sensitivity can be maintained via mine control rooms minimising on site tampering and human error.
Benefits
- Improves staff safety by minimising high-energy GET ejections
- Increases safety as personnel are not required to enter the crusher to recover tramp metal.
- Minimises production delays and downtime due to crusher blockages and damage
Status
This technology has been trialed at a prototype development stage and shown to detect tramp metal in a 12m3 bucket at iron ore mines in Western Australia and South Africa. Current research focuses on a pre-commercial system deployable in a CAT 992 with a detection capability of more than 50% across the face of the bucket.
The next stage of development will target more than 50% detection capability in a CAT 993 bucket. Future work will aim to provide a minimum of 50% detection capability in bigger front-end loaders, excavators and shovel buckets.
Mining3 is still seeking engagement with mines experiencing tramp metal issues for potential prototype implementation and validation test sites.
Partners
Mining3 is working with ESCO, an equipment metal parts manufacturer, to incorporate the uncrushables detection technology into their bucket design and the future commercialisation of the technology.
Factsheet
Access the latest detection of tramp metal factsheet.